Machine Monitoring
Spindles nowadays reach very high working speeds. Machining processes often cause considerable vibrations. These lead to poor product quality and to bearing damage to spindles and axes.
Early detection of bearing damage is essential to keep machine and spindle vibrations under control, reduce consequential costs and improve quality. This can be achieved by precise evaluation of sensor signals (vibration, temperature and optional gravity). Alarm limits can be set individually, and in the event of exceeding or dropping below them, a defined reaction can be taken at an early stage.
Artis monitoring systems indicate problems of the machine condition after a tool change at an early stage before the cutting process. When changing tools, a chip can enter the space between the tool holder and the main spindle. If this event occurs, the quality of the workpiece to be machined is often affected. Usually, the result of the chip placement is only determined at the end of the entire machining process when the workpiece is inspected. Real-time detection with Artis machine monitoring systems means avoiding all unnecessary subsequent steps and saving a considerable amount of time.
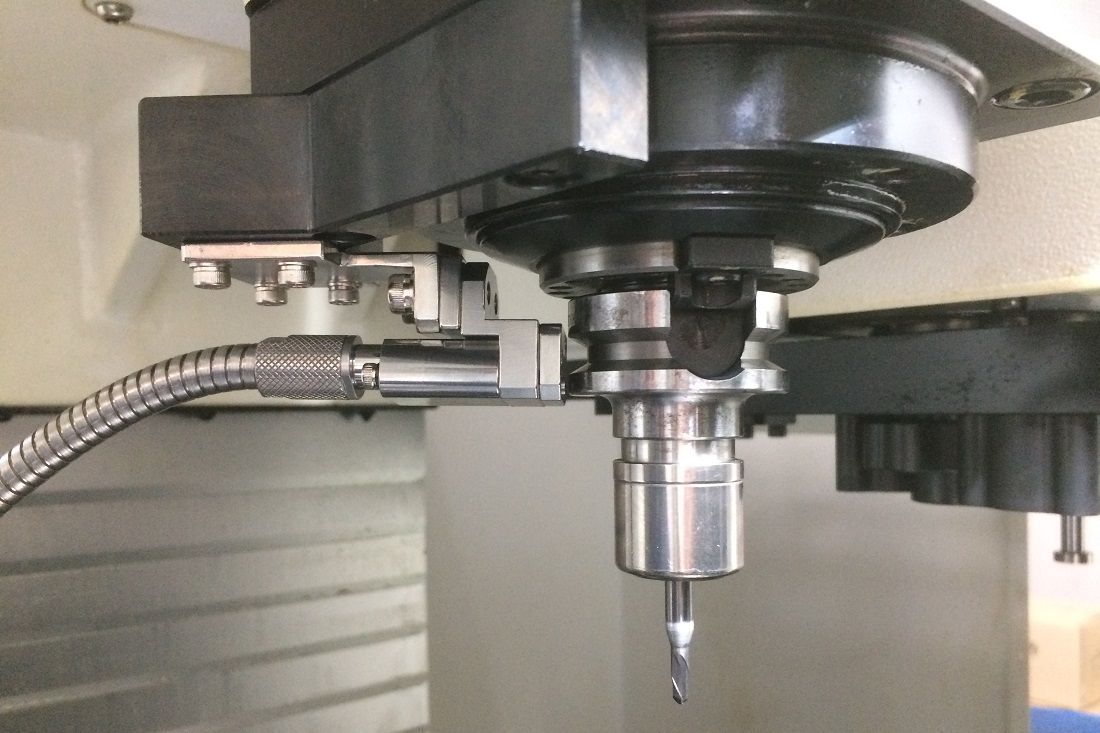
- Artis machine monitoring systems reliably detect vibration anomalies and tool holder run-out after tool change
- Vibration sensors measure bearing conditions of spindle and axis
- Easy integration into new or existing machine tools, equipments or robots, independent of machine control type
- The system can run permanently in the background. Operator interventions are only necessary in case of alarm
- The event recorder (blackbox) reliably records the alarm events (date, time and values) and stored information can be used for further evaluation and analysis
- The sensor data and the event data can be exported as CSV file
- Reduces unplanned outage times and costs because worn components can be replaced at an early stage (predictive maintenance)
The compact systems consist of an electronic module, a sensor and a software package for configuration, visualization and data management. Integration into new or existing machines and systems is simple. The module is installed on a DIN rail in the control cabinet or in a field housing.
The vibration and eddy-current sensor are mounted at a suitable location in the machine. The handshake with the machine control is carried out via IO-connection and can therefore be used independently of control type. Access and data visualization is carried out via the Ethernet connection from a WINDOWS-based system, such as an industrial PC or machine control panel, but can also be performed directly on a SIEMENS TCU (LINUX) control.
For stand-alone use or as part of the GENIOR MODULAR process monitoring system:
- GEMVM Vibrations- and Temperature monitoring system and Visu plug-in software
- GEMRO Tool Holder RunOut Detection system